The Perforce Difference
Healthcare organizations face the daunting task of maintaining profitability while complying with regulatory mandates such as HIPAA. Perforce provides a platform to gain a competitive edge, meet compliance every time, automate manual processes, and test software more quickly.
Express Scripts Saves $2M+ and Accelerates DevOps and Data Compliance
After decades of mergers and acquisitions, Express Scripts’ infrastructure was cobbled together with no DevOps practices in sight. Watch how they turned it around.
Healthcare Providers
Healthcare providers must maintain profitability while complying with regulatory mandates such as HIPAA, ICD-10, Meaningful Use Stage 1 and 2, and more. Perforce simplifies and accelerates the software testing and development process, to reduce risk and help ensure compliance. Manage and automate testing assets, streamline traceability, and improve visibility throughout your testing and software development efforts.
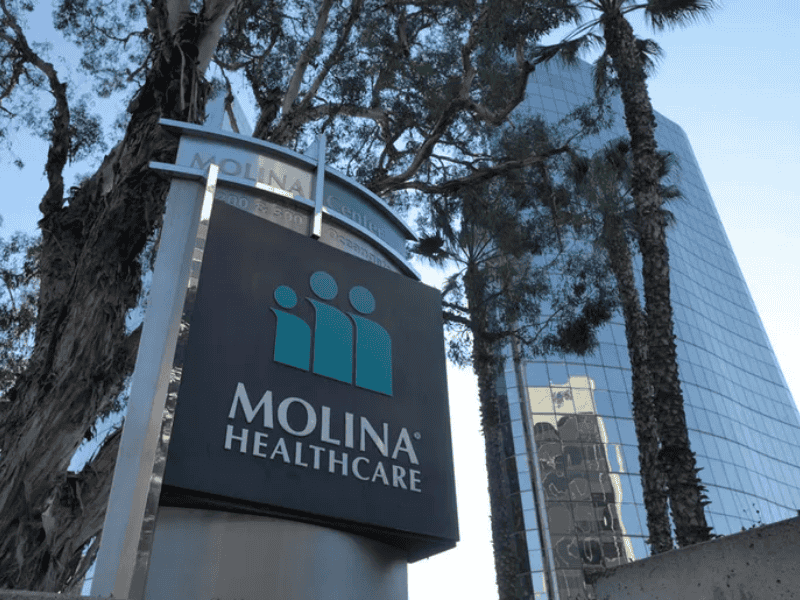
Molina Healthcare Cuts App Development Time in Half and Saves $10M
Fortune 500 company Molina Healthcare needed to update its infrastructure as the U.S. government overhauled its healthcare system. Molina turned to Perforce for accelerated application development and more advanced reporting and analytics. Projects that took six months can be completed in half that time with millions of dollars in storage costs savings.
Don't Sacrifice Speed or Quality
- Move, manage, and secure data to the cloud or on-premises.
- Deploy and update claims processing systems more quickly.
- Automatically identify PII and PHI, mask patient information, and safely share data with partners, all while complying with data privacy mandates such as HIPAA and GDPR.
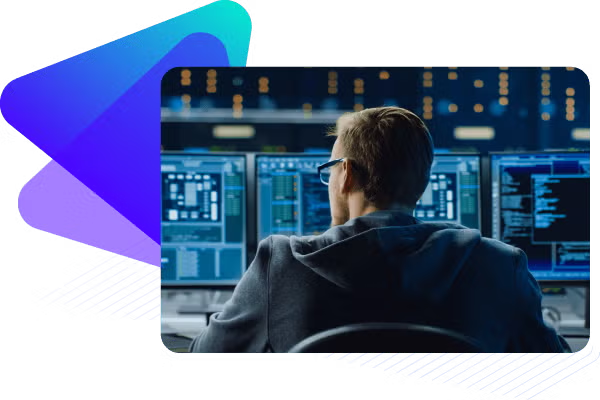
- Eliminate hours of manual effort with instant traceability for simplified compliance.
- Eliminate gaps in test coverage and attain a single source of truth.
- Gain deeper insight into the impact of changes with real-time data visibility.
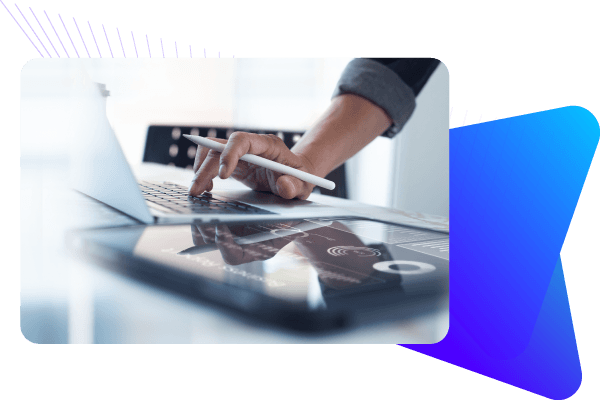
- Focus on high-level engineering needs vs manual tasks.
- Make changes in hours vs weeks for compliance, security, and patching needs.
- Understand what is happening with your infrastructure and how to remedy it.
- Automate application and OS management post-deployment for seamless experiences.
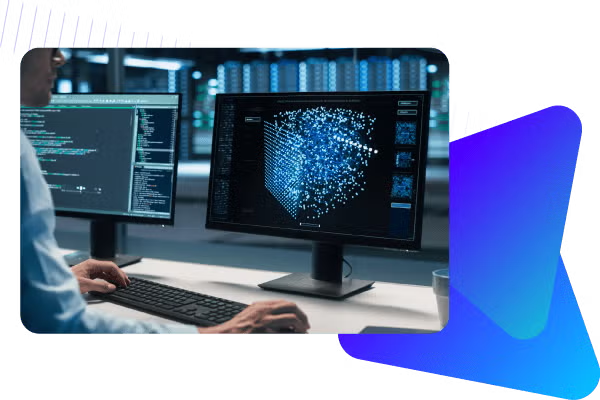
- All-in-one continuous testing platform offers seamless customer experiences.
- Protect sensitive data with advanced data management techniques.
- Detailed reports and analytics for metrics related to response time and error rates.
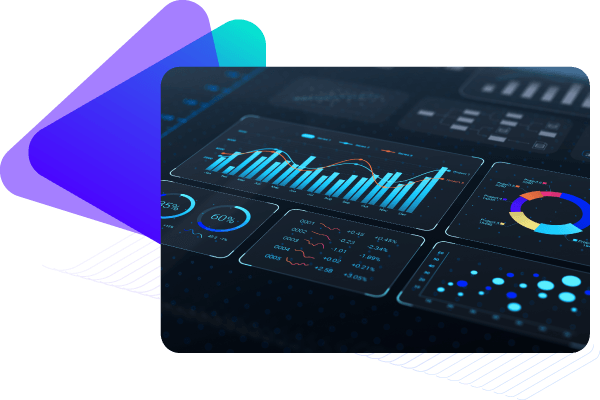
- Flag rule violations as soon as they occur and remain compliant with functional security and secure coding standards.
- Produce comprehensive compliance reports for security audits.
- Keep up with evolving FDA, government and industry cybersecurity regulations and verify the security and quality of your software early in development.
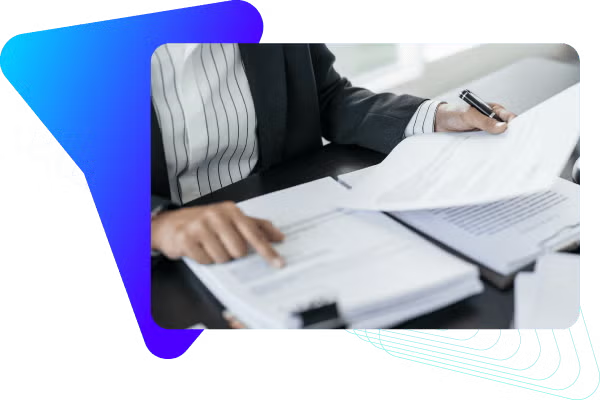
Medical Devices
Medical device development companies use Perforce to ensure continuous traceability across the product design and development lifecycle, and enforce compliance with the highest safety and regulatory standards.
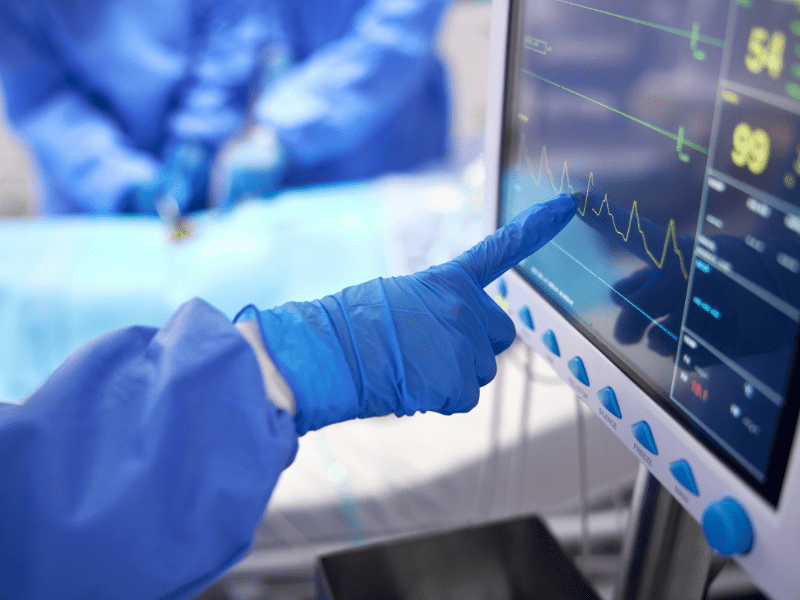
Fractyl Health Easily Achieves Medical Device Compliance
Medical device compliance was critical to patient safety but was time-consuming for the team at Fractyl Health. They needed a solution to create a traceability matrix that met FDA and ISO standards, and that would get them to compliance and CE certification.
Detect Issues Early and Remain Risk Adverse
- Automatically create a traceability matrix to easily prove FDA and ISO compliance.
- Manage requirements, tests, and issues, and ensure all requirements are tested and fulfilled.
- Perform risk analysis including FMEA and impact analyses to mitigate risk.
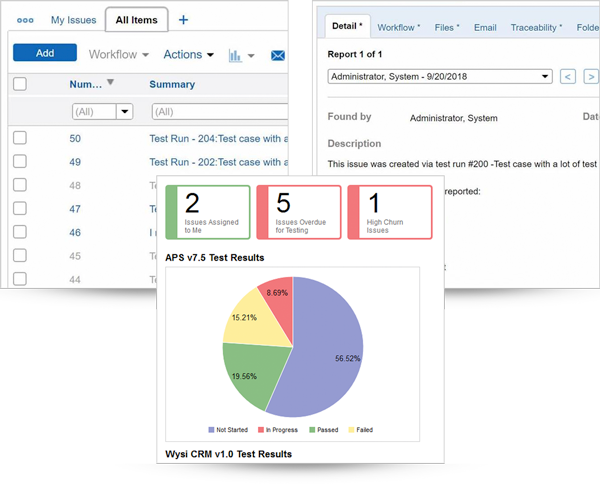
- Tame design complexity with an IP management and collaboration platform that tracks IP and its metadata across projects for end-to-end traceability.
- Collaborate globally and establish design verification traceability for compliance with Medical Device Manufacturing Standards.
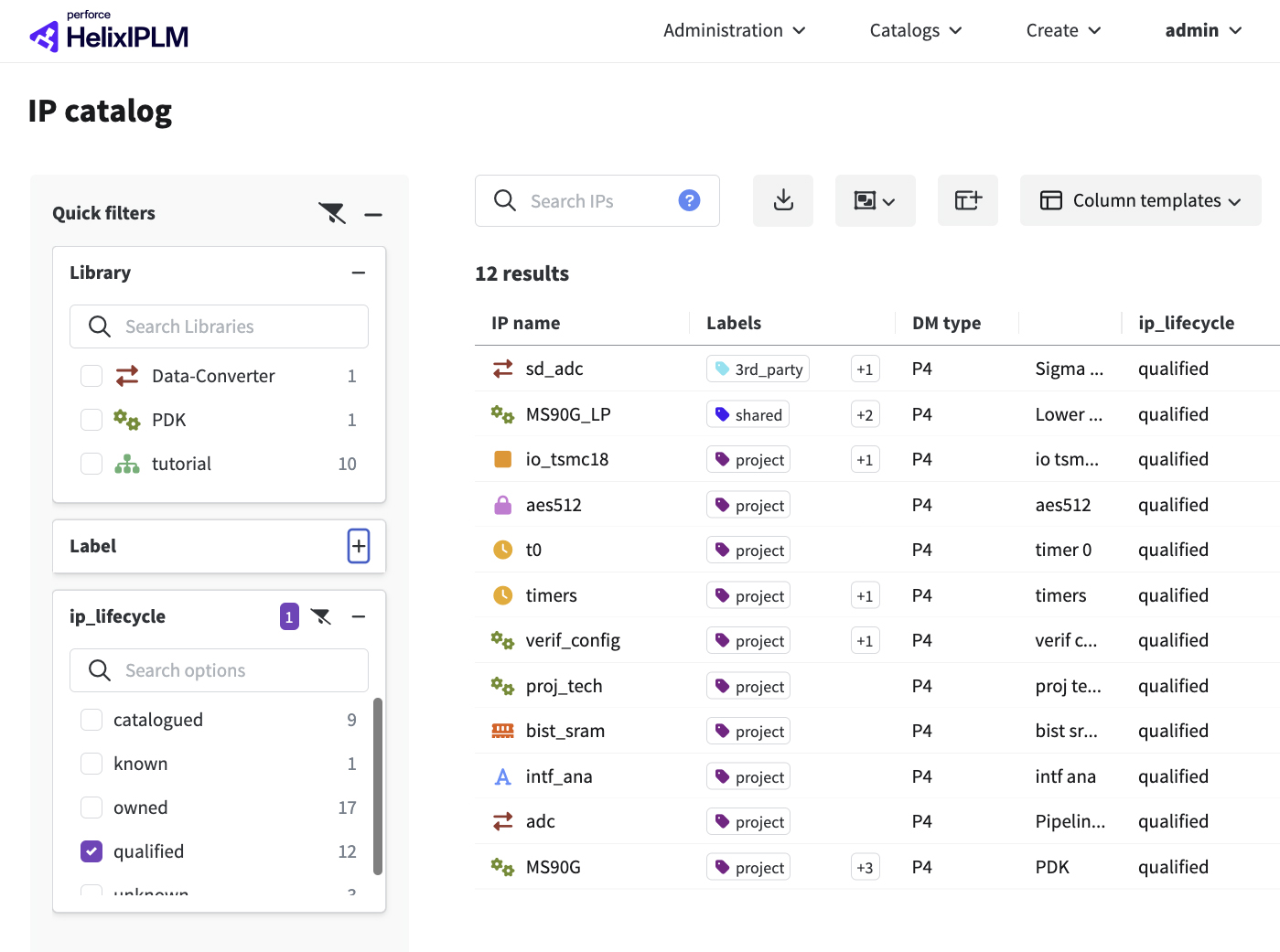
- From medical device designs to embedded code, use a version control software to securely version your digital assets.
- Track every change ever made.
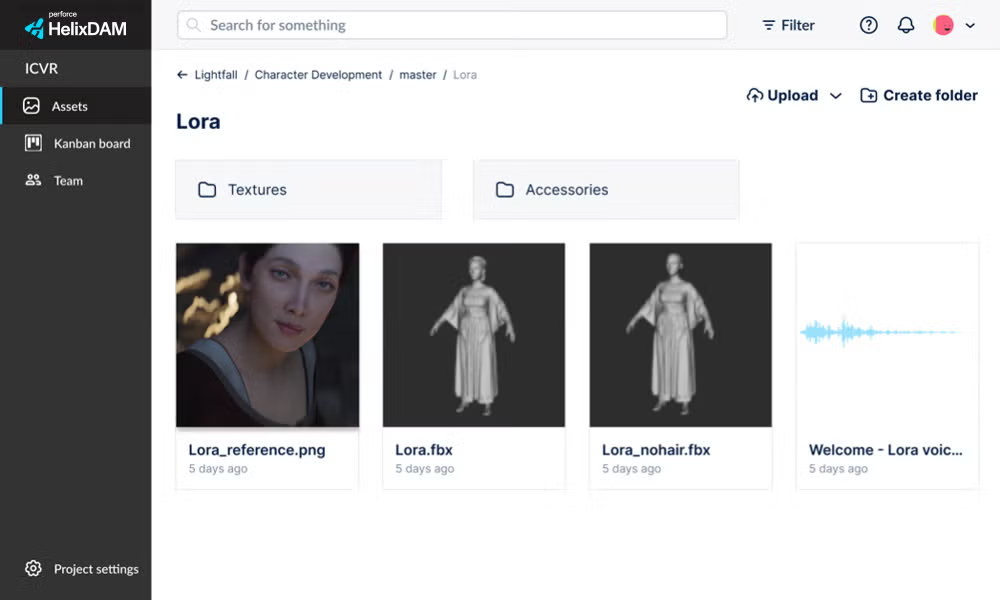
- Shift security to the left: Find and fix defects early in development, when they’re easier to fix, less expensive, and not life-threatening.
- Streamline DevSecOps with CI/CD tool, container, cloud service, and machine provisioning integration.
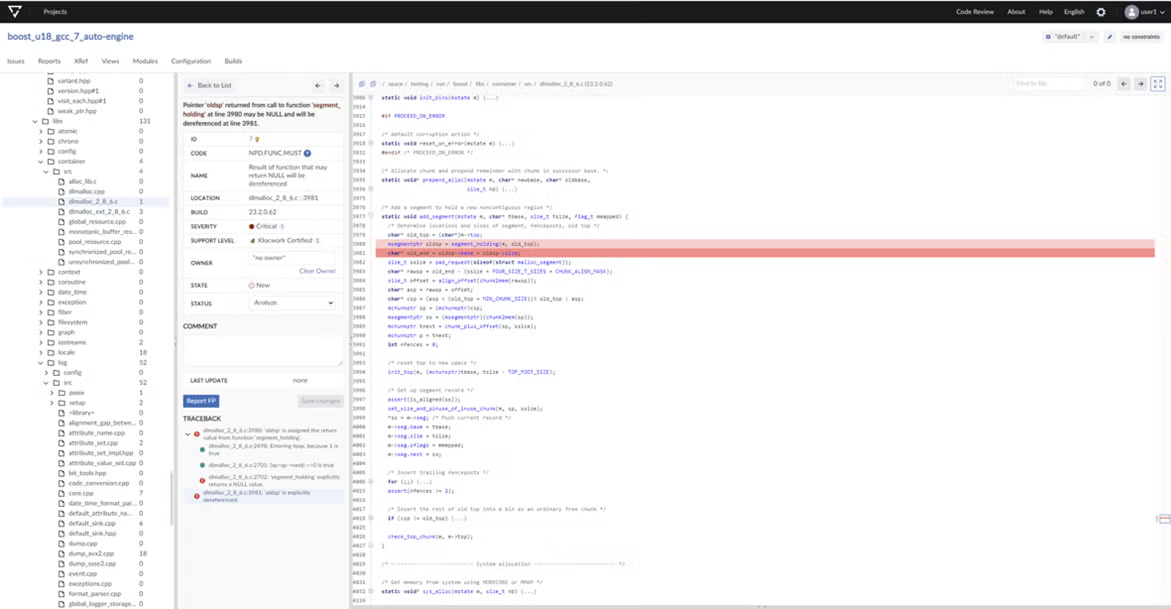
Comply With Medical Device Manufacturing Standards
Medical devices must be manufactured without error and comply with industry standards.
IEC 62304 specifies lifecycle requirements for medical devices and medical device software.
ISO 13485 specifies the quality management requirements for medical devices.
ISO 14971 is the risk management standard for medical devices.
Several FDA regulations are also applicable to medical devices, including 21 CFR Part 11.
European Medical Device Directives are required for selling medical devices in the European Union. Compliant devices receive a CE Mark.
Health Insurance
Health insurance companies are under pressure to keep patient data secure and compliant with industry regulations, and provide user-friendly web and mobile portals for patients to easily access their healthcare data — without downtime.
Delight Customers Across Platforms While Keeping Data and System Integrity Secure
- Move, manage, and secure patient data in the cloud or on-premises.
- Deploy and update claims processing systems faster and more efficiently.
- Identify and mask PII and PHI to comply with security mandates.
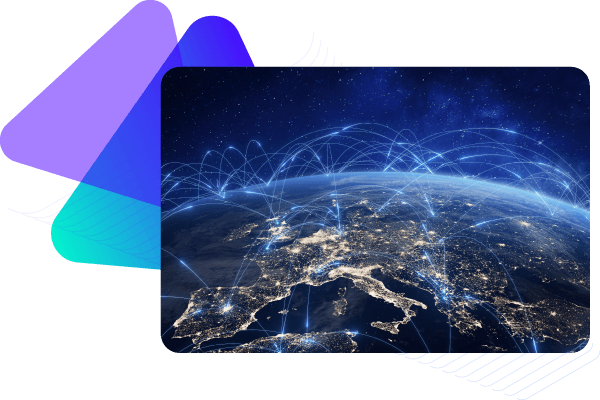
- Reduce manual effort with instant traceability for simplified compliance.
- Eliminate gaps in test coverage and maintain a single source of truth.
- Gain real-time insights into changes with data visibility tools.
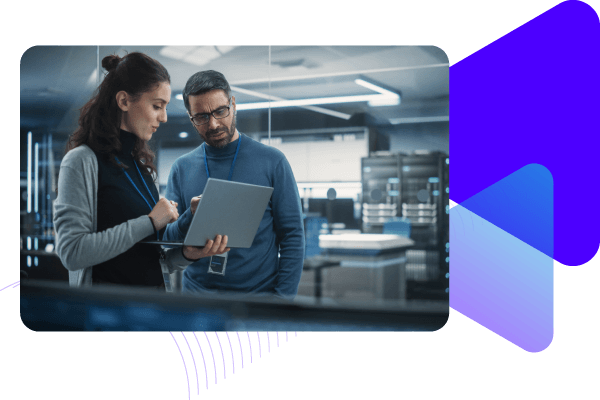
- Eliminate the reliance on fragile locators and script updates to automatically evolve UI experience across platforms without effort.
- Utilize natural l language prompts so anyone on the team can test.
- Protect sensitive data with advanced security features.
- Gain deep insights with real-time analytics.

- Ensure security policies are automatically updated.
- Cut down delivery time by stopping slow, cumbersome manual processes.
- Improve confidence and response time in security, compliance, monitoring, and alerting.
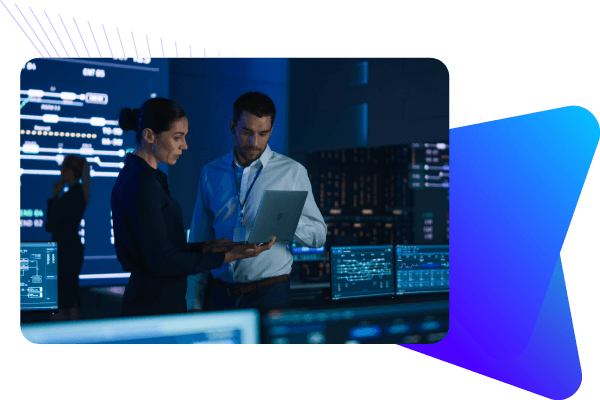
Proven Performance
High-priority incidents plummeted when LV= moved to Perforce Puppet.
4/5
Top Healthcare Insurance Providers Choose Perforce
From Days to Minutes
With modernized development and testing.
“For every new app, we had to manually provision the servers with the required controls and middleware. It’s now automated. It takes the burden off of us."
– Mohinder Singh, Senior Cloud DevOps Engineer, Guardian Life
Outperformers Prevail With Perforce
Perforce delivers a DevOps Edge to the world’s outperformers, empowering them to build, manage, and maintain high-stakes applications — from code to business-ready.
View Customer Stories
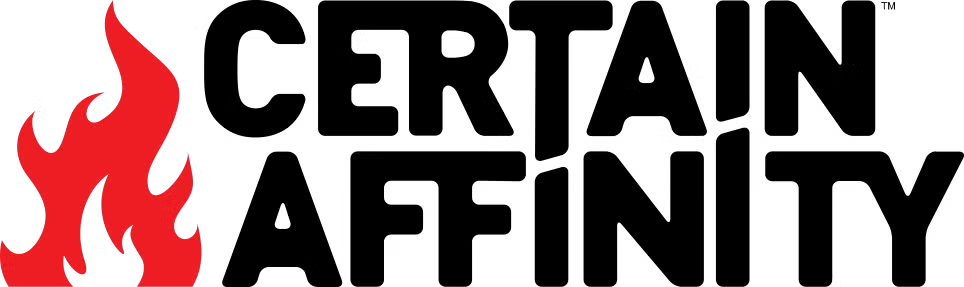
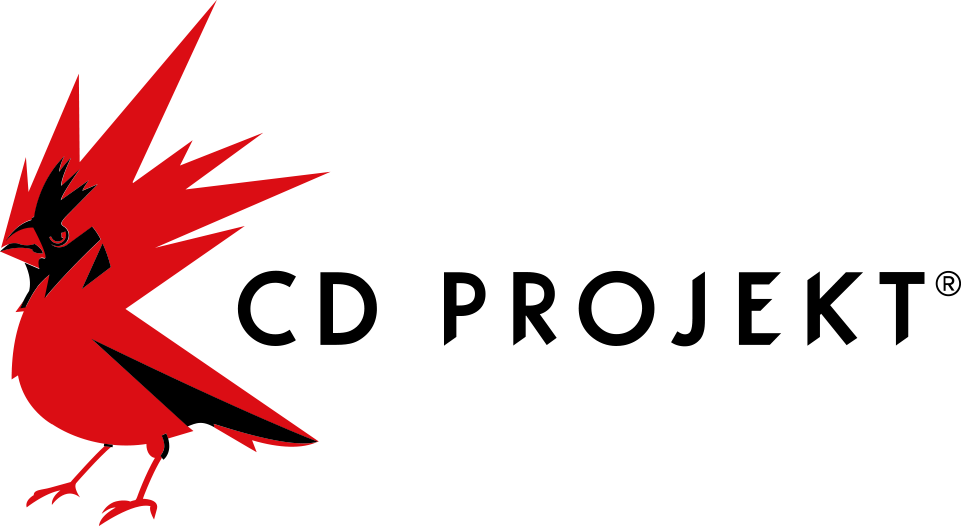
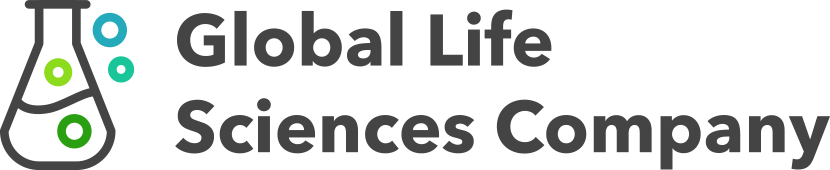
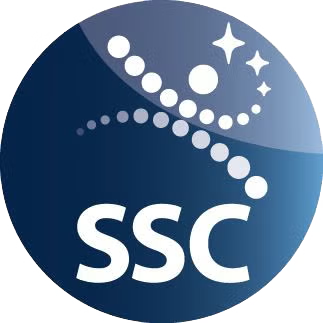
Get the Power of Perforce Today
Embrace complexity, achieve speed without compromise, improve security and compliance, and run your DevOps toolchains with full integrity.